Elastomerverarbeitung
Eine Kautschukmischung besteht aus einer Vielzahl an Komponenten, die in einem Mischprozess möglichst homogen vermischt werden sollten. Häufig werden neben einen Kautschuk mehrere Kautschuke zu einem Blend vermischt. Das Ziel ist es, definierte, anwendungstechnisch relevante Eigenschaften für spezielle Anwendungen zu erzielen. Die anwendungsrelevanten Eigenschaften eines Elastomerbauteils sind grundsätzlich vom Herstellungsprozess abhängig. Technologische und stoffliche Faktoren beeinflussen die Qualität der Mischung. Wir unterstützen Sie gerne bei Forschungsprojekten und beraten Sie bei der Gestaltung der Mischungsrezeptur und den Mischparametern.
Im diskontinuierlichen Mischverfahren können wir für Sie Mischungen (~ 50 – 60 g) herstellen und hinsichtlich der Vulkanisationskinetik und der mechanischen und viskoelastischen Eigenschaften untersuchen.
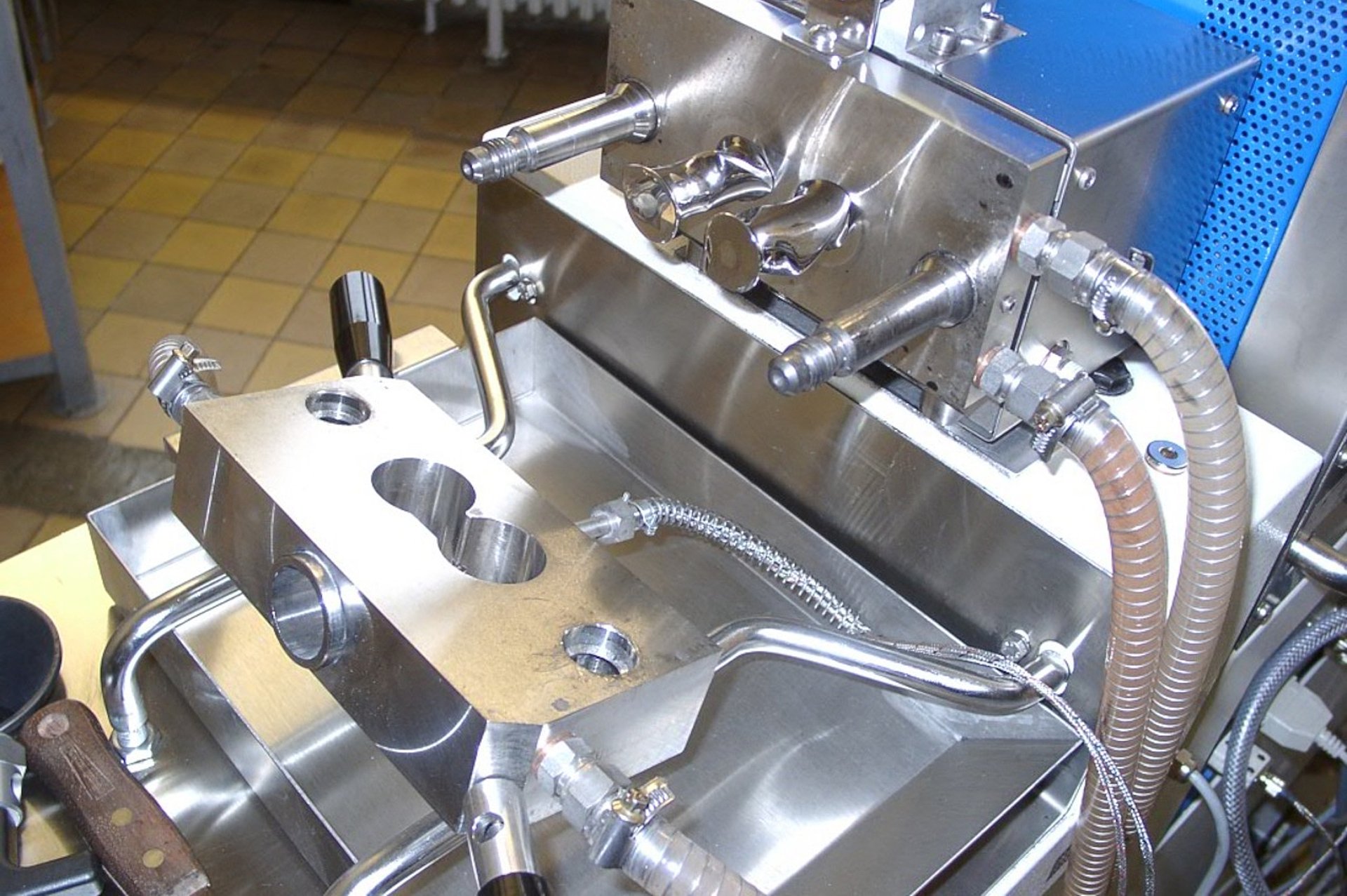
Grundlagen
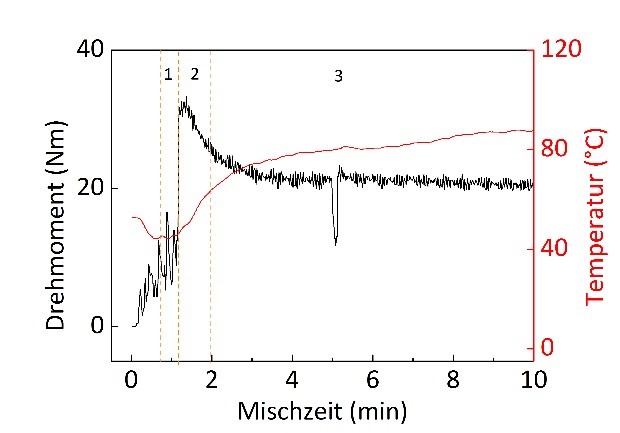
Kautschukmischungen sind Gemische aus einer großen Anzahl an Bestandteilen, wie Polymer, Füllstoffen, Weichmachern und verschiedensten Chemikalien, die die Endeigenschaften des daraus hergestellten Vulkanisats entscheidend bestimmen. Um eine gleichbleibende Mischqualität realisieren zu können, ist ein reproduzierbarer Mischprozess von größter Bedeutung.
Unter Mischen versteht man das Verteilen und Zerteilen von mindestens einer Komponente in einer anderen, wobei sich die Komponenten hinsichtlich ihrer Eigenschaften unterscheiden. Weiterhin unterscheidet man zwischen distributivem und laminarem Mischen. Bei ersterem werden durch eine aufgebrachte Kraft die Komponenten gegeneinander bewegt, sodass im Laufe der Zeit eine Durchmischung erfolgt. Man spricht dabei von einem statischen Prozess, bei dem die einzelnen Partikel ihre Größe nicht verändern. Von einem laminaren Mischen wird gesprochen, wenn die zu vermischenden Komponenten viskoelastische Flüssigkeiten oder zumindest deformierbare Substanzen sind.
Eine Kautschukmischung besteht aus einer Vielzahl an Komponenten, die in einem Mischprozess möglichst homogen vermischt werden sollten. Das Ziel der beabsichtigten Variation der Mischungsbestandteile ist es, definierte, anwendungstechnisch relevante Eigenschaften für spezielle Anwendungen zu erlangen.
Zu Beginn des Mischprozesses werden Kautschuk, Füllstoff, Weichmacher, sowie Hilfs- und Zusatzstoffe zu unterschiedlichen Zeiten in den Innenmischer eingefüllt. Sobald die Mischkammer, durch das Herabsenken des Stempels geschlossen wurde, beginnt der Mischprozess. Der einwirkende Druck auf die Mischungsbestandteile steigt, was zum Anstieg der Temperatur führt. Das Polymer wird fließfähiger und beginnt die Hohlräume des Füllstoffs auszufüllen (Infiltration). Es bilden sich Polymer-Füllstoff-Agglomerate, die zu einer Viskositätserhöhung führen. In Folge von einwirkenden Druck-, Scher- und Zugspannungen während des Mischens werden die größeren Füllstoffagglomerate zu kleineren Aggregaten zerteilt, die mit fortschreitender Mischzeit in der Polymermatrix zerteilt (Dispersion) und verteilt (Distribution) werden. Unterschreiten die wirksamen Spannungen, aufgrund von starker Viskositätsabsenkung infolge einer Temperaturerhöhung oder Polymerabbau einen kritischen Wert, dann nimmt die Zerkleinerung der Agglomerate ab.
Anhand des Verlaufs der Drehmoment-Zeit-Kurve kann der Zeitpunkt der Füllstoffinkorporation und der -dispersion verfolgt werden. Nach dem Absenken des Stempels kann ein Anstieg des Drehmoments bis zu einem Maximum beobachtet werden (Bereich 1). Bis zu diesem Zeitpunkt werden die Mischungsbestandteile durchmischt. Die Füllstoffoberfläche wird in dieser Phase von den Polymerketten benetzt. Erreicht das Drehmoment sein Maximum (Bereich 2), dann ist der Füllstoff in die Polymermatrix vollständig inkorporiert. Dieses Drehmomentmaximum wird auch als „Black Incorporation Time (BIT)“ bezeichnet.
Gerätetechnische Ausstattung
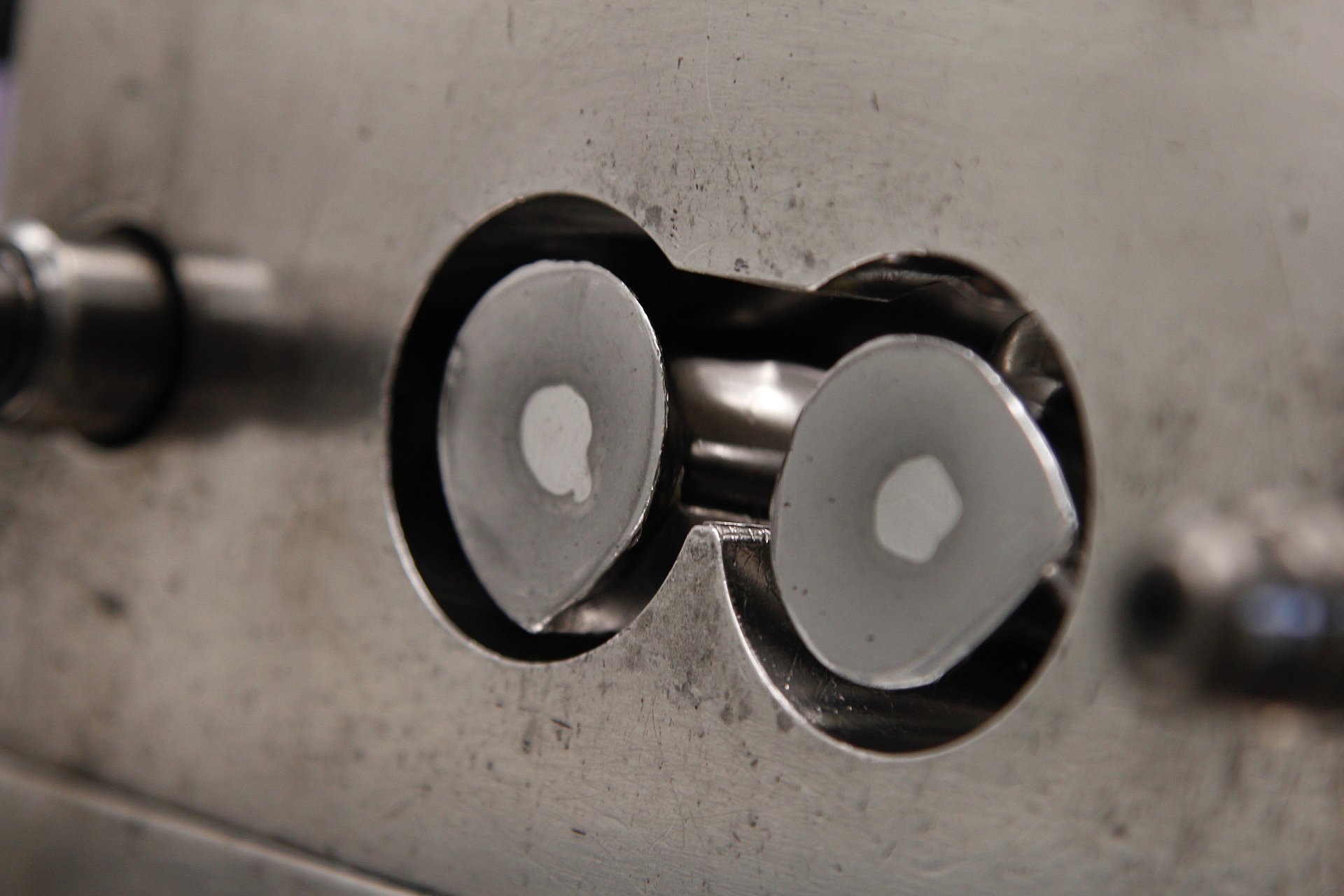
Laborinnenmischer
- Kammervolumen: 75 cm³
- Knetschaufeln: Banburry
- Temperatur: bis 300 °C
- Maximales Drehmoment: 40 N
- Aufnahme von Drehmoment-Zeit- und Temperatur-Zeit-Diagrammen für Mischungsherstellung
- Reproduzierbare Ermittlung der Black Incorporation Time (BIT) nach Cotten
- Erstellung temperaturkorrigierter Drehmoment-Zeit-Kurven
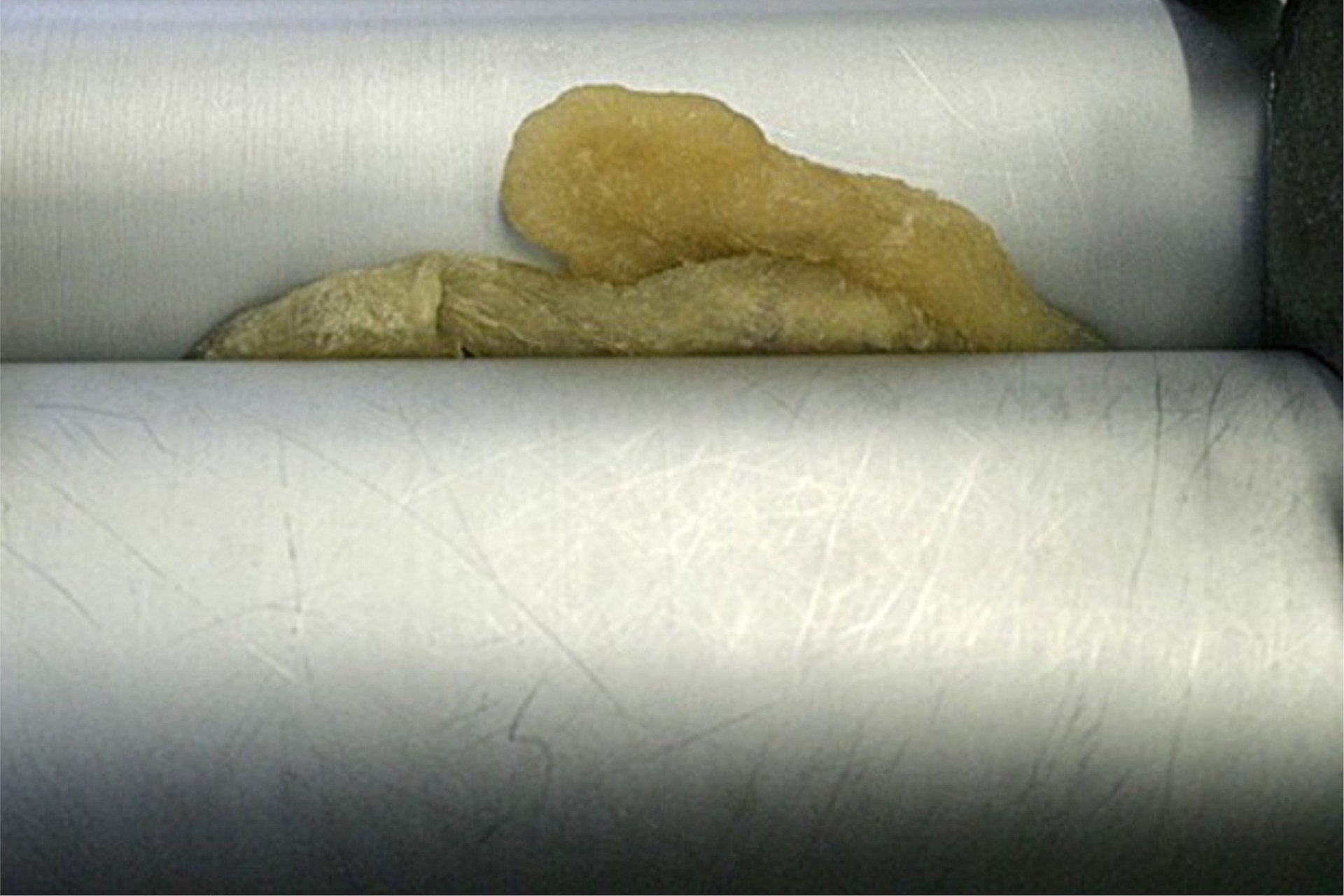
Laborwalzwerk
- Homogenisierung und Compoundierung von Kautschukmischungen
- mechanisch-thermische Beanspruchung und Aktivierung von Gummimehl
Dr. Katja Oßwald
Telefon: +49 (0)3461 30889-72
E-Mail schreiben